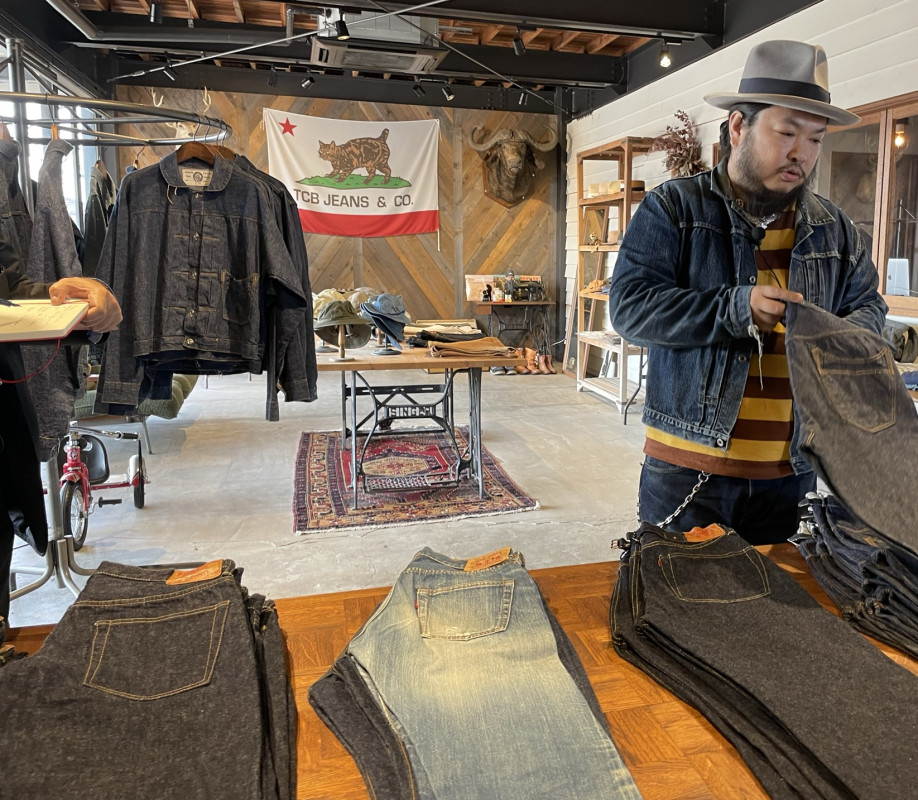
July 10, 2024
Japanese Denim: Perfection in Blue
Exploring Japan’s denim industry
The world of denim is one massive rabbit hole to wander down, and to the uninitiated, it also can be an intimidating one—including that of Japanese denim. Websites written by and for so-called “denim heads” brim with jeans-related terms like slub (coarse/bumpy textural irregularities), nep (protruding white cotton fibers), and deadstock (pre-1990s pieces with their original tags intact).
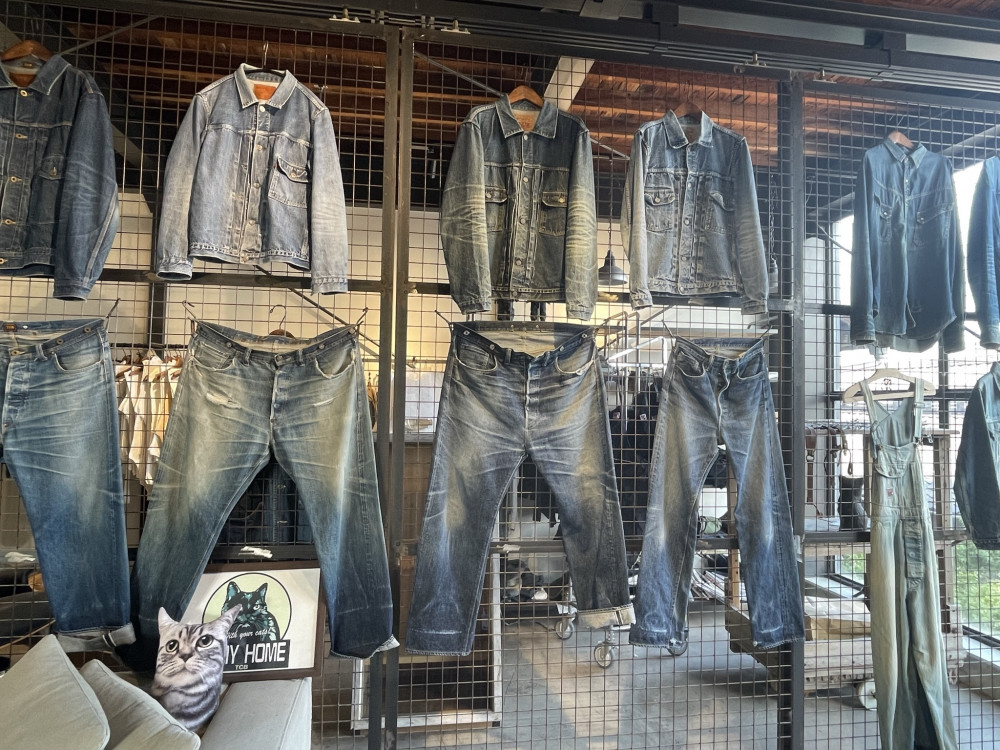
“Denim jeans served as something of a countercultural symbol within conformity-bound Japan. “
Besides providing ample opportunity to geek out on new terminology, learning more about denim is a pursuit that requires taking a deep historical dive—and the history tying together Japan and the United States with respect to this fabric is a storied one indeed. This account is relayed poignantly in the 2016 documentary Weaving Shibusa, where legends in the world of Japanese denim recount their love affair with American jeans beginning during the postwar period when Japan experienced a 180° about-face that involved largely embracing its former enemy’s culture.
Love Japanese fashion? Check out our “Tokyo Trends” series to get the latest looks for yourself
Amidst this story, denim jeans served as something of a countercultural symbol within conformity-bound Japan. The garment was seen onscreen in Hollywood films, and also literally in the flesh—with the used jeans worn by U.S. occupation military servicepersons finding their way into the underground markets of Tokyo’s Ueno district. Plus they were at used clothing and import stores like the ones in Osaka’s American Village.
Speakers in the film also probe their feelings of intrigue into those who originally wore their coveted vintage denim jeans: Were they bikers? Farmers? What were their lives like?
Weaving Shibusa additionally recounts the denim revival launched in Japan during the 1980s and 1990s—after the garments became subject to mass production—prompting denim-obsessed makers to bring back the unique character of vintage American-style jeans.
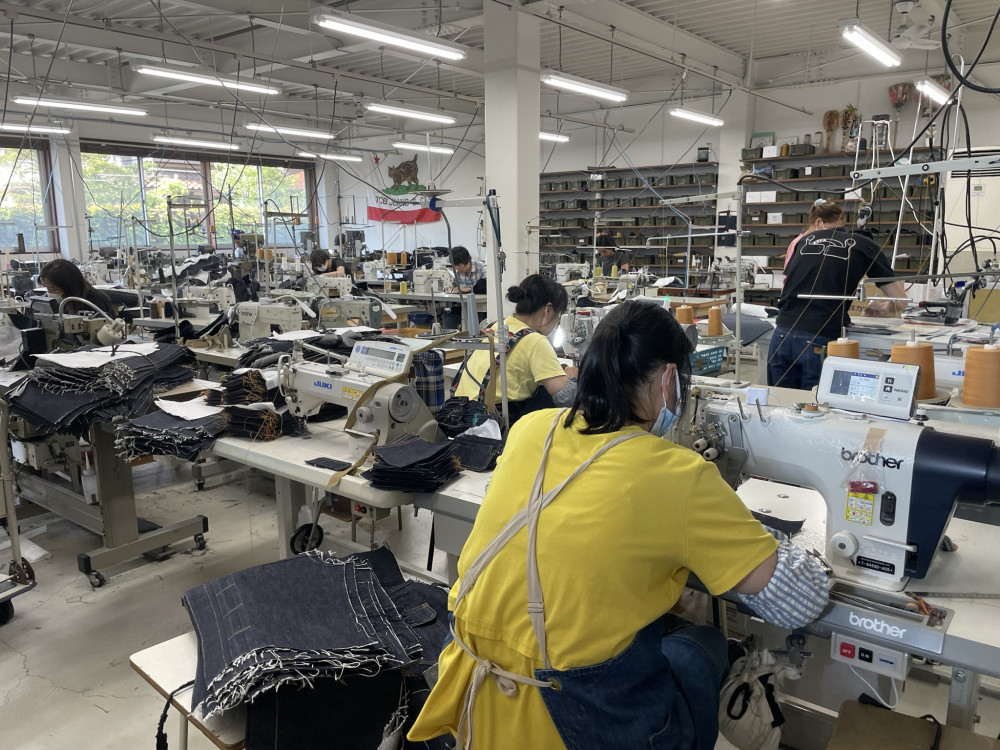
Key players in this story include Japan’s denim experts such as Iron Heart founder Shinichi Haraki, who cuts a James Deanesque figure of the rugged, burly individualist, and whose heavy denim is perfect for road-loving motorcyclists like himself; and members of the famed Osaka Five, whose brands (Denime, Warehouse, Studio D’Artisan, Fullcount, and Evisu) are legendary within this history.
“While the ancient art of indigo dyeing exists globally, Japan has paid particular attention to respecting and preserving it.”
As these and other Japanese manufacturers began to imitate brands like Levi’s and Lee jeans, competition ensued between the U.S. and Japan with respect to denim jeans, as it also did within other manufacturing sectors, like guitars and automobiles. And naturally, superior products often ensued in Japan due to its meticulous monozukuri-style craftsmanship—as well as its deep history in related industries.
Kojima Jeans Street: A district steeped in indigo blue
In the city of Kurashiki, Okayama Prefecture, where the Seto Ohashi Bridge connects Honshu and Shikoku islands, lies a famed attraction known as Kojima Jeans Street. Established in 2009, its story similarly has roots that date back far earlier. Part of the sea until land reclamation formed the city around 400 years ago, rice was unable to grow there due to the land’s high salt content. This led to the cultivation of rush grass and in turn to thriving industries of cotton, textiles and indigo dyeing—a perfect recipe for denim jeans.
You might also be interested in: The preservation and resurgence of the treasured fabric and cotton craft kurume kasuri
Japan’s first domestically-produced jeans came courtesy of the Big John company in Kojima in 1965, but the area did not take off as a jeans center until decades later. As Japan’s denim revival spread from Osaka, many replica jeans manufacturers began to establish themselves in Kojima during the 1990s and onward. Central to the revitalization of the area—and the launching of Kojima Jeans Street—was Isao Manabe of the Japan Blue group, who created the famed Momotaro Jeans.
Undertaking all weaving and indigo dyeing processes by hand, he notes that while the ancient art of indigo dyeing exists globally, Japan has paid particular attention to respecting and preserving it—thereby contributing to the prestige of Japanese jeans manufacturing (as well as the price tag that accompanies such labor-intensive methods).
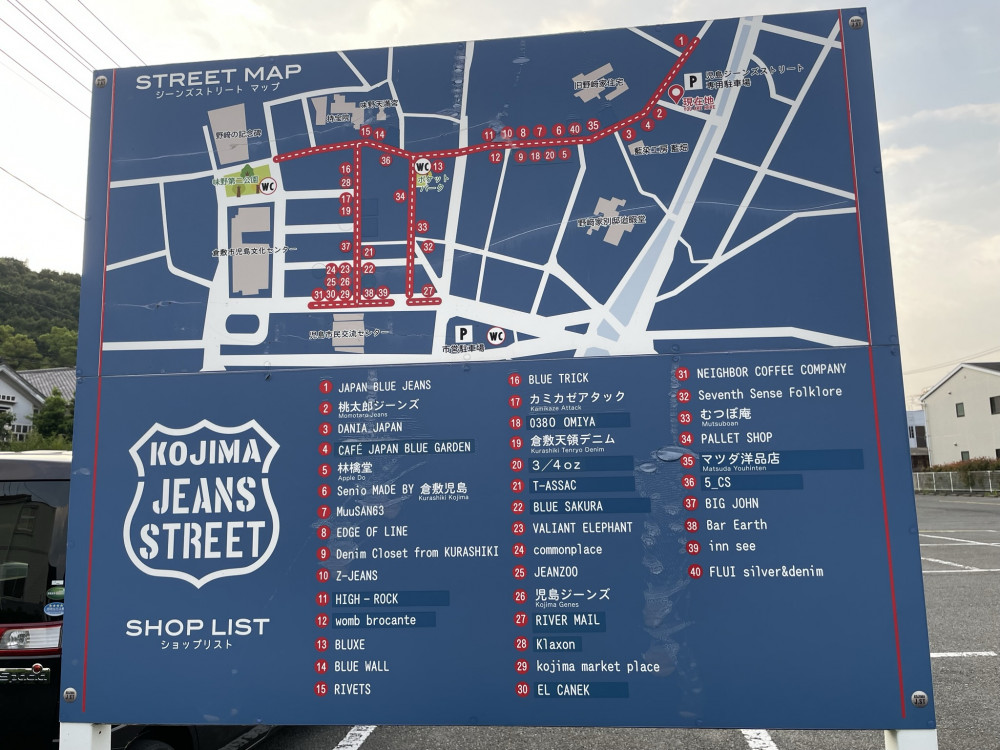
Denim and wartime history
Other notable denim companies in Kojima include Howa, which undertakes a process of natural pumice stonewashing; and TCB Jeans, run by another demi-god in Japan’s denim community, Hajime Inoue. A Hiroshima native, Inoue relocated to Kurashiki around 20 years ago to pursue his dream of crafting quality reproductions of American denim jeans on a small-scale basis—specializing in ultra-rare models such as 1940s Levis, which include characteristics such as different stitching, or missing flaps.
“Because most factories in the United States were used for military purposes during the war, jeans makers hired unskilled workers—thereby resulting in numerous irregularities,” he explains. “And because metal was needed for the war effort, the normal five buttons were actually limited to four in those 1943-1946 models; hence their attractiveness as collectors’ items.”
“Retail operators in the U.S. are today favoring Japanese denim jeans for their impeccable quality.”
Inoue named his company TCB after the American phrase “taking care of business,” which he admires for its “no-nonsense, get it done right”-style philosophy; and also as the “Two Cats Brand” in a nod to his own two felines, while also paying playful homage to his beloved Levi’s jeans by riffing on their two-horse logo.
A dedicated sewer, Inoue’s skills are also in high demand due to his deft abilities with the old U.S. shuttle sewing machines used widely in Japan during the 1960s, which most young people in both countries are unable to repair.
Japanese denim coming back full circle
And just as these denim manufacturers in Japan based their products on American originals, retail operators in the U.S. are today favoring Japanese denim jeans for their impeccable quality.
One such store is Cave + Post in Phoenix, Arizona, whose selection includes men’s fashion items, colognes, cowboy-style hats and belts—and Hiroshi Kato jeans. According to store owner Patrick Burch, Hiroshi Kato “produces selvedge denim in their factory outside Tokyo on vintage shuttle looms, and then imports the fabric to Los Angeles where everything is cut and sewn.”
“From start to finish, Kato has an amazing hands-on approach,” Burch explains. “From inspecting the rolls of denim before hitting the production line to the final product—from the stitching to the hardware to the hidden bar tack in the hip pocket that follows vintage tradition—every detail is intentional.”
And as for the future of Japanese denim? According to at least one expert in the Weaving Shibusa documentary, perfection may have already been achieved, as there may be nothing else like it that ever comes along again.